Manufacturing | BIRN
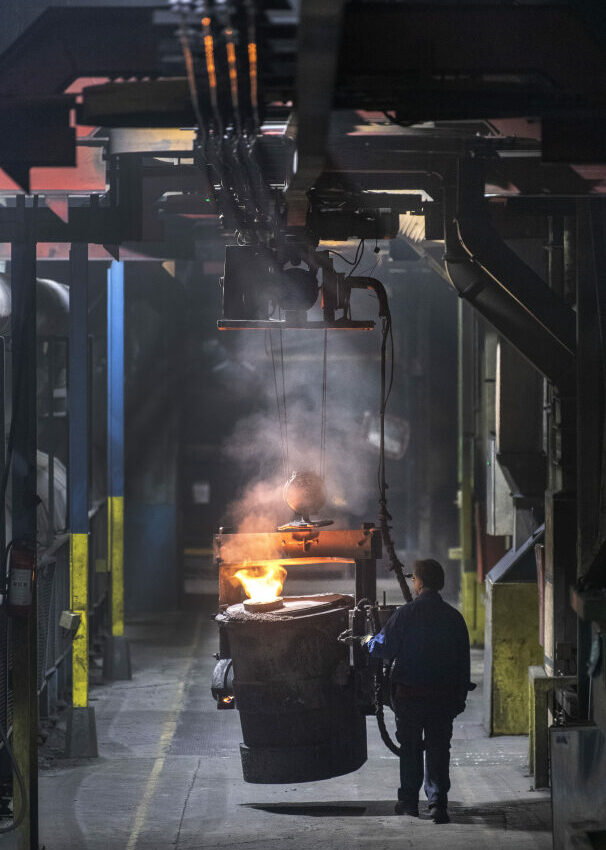
Leveraging manufacturing data in cast iron production
to meet sustainability targets.
BIRN is one of Northern Europe’s largest foundries, consuming enormous amounts of energy in the process of melting and forging various cast iron items. In a collaborative innovation project completed in 2022, BIRN and Init worked together to leverage manufacturing data to lower energy consumption, reduce carbon emissions, and increase employee engagement.
Energy efficiency as a top priority
Energy efficiency has always been the main goal in the eyes of Lars Jørgensen, CTO at BIRN. “The advantages of emphasising energy efficiency are numerous” says Lars Jørgensen, adding that by using that as a compass, they can keep staff members concentrated on process improvement.
Focusing on energy efficiency allows us to get the most out of our efforts and investments, regardless of whether the cost of energy is high or low.
Lars Jørgensen
It was the ambition of getting the most out of the company’s energy consumption that in 2021 lead BIRN to initiate a collaborative innovation project with Init and other partners. The purpose of the project was to gain better data insight which can help BIRN make the right decisions for minimising its energy consumption and climate footprint significantly.
Init’s data engineers have worked closely with BIRN to collect and analyse energy and manufacturing process data from the induction furnaces and other manufacturing equipment.
With the opportunities for data collection that are available now for manufacturing equipment and production parametres, we have better conditions than ever before for providing customers with an overview of and insights into their production processes and energy consumption.
Henrik Dam from Init.
“BIRN’s goal of bringing its many different data sources into one horisontal platform, significantly increases their ability to create value in regards to both production, economy and environment. This fits well with Init’s philosophy of bringing data to life”, he concludes.
Experimenting to achieve energy optimisation
With a yearly energy consumption in excess of 100 GWh, there is some potential to work with at BIRN. “The major part of energy consumption comes from the melting processes”, says Lars Jørgensen.“From surveys conducted by our furnace manufacturer, we know that, under ideal conditions, approximately 560 kWh of energy is required to melt scrap metal into one metric ton of molten iron. This is a baseline we use to benchmark our performance after.”, Lars Jørgensen continues.
During 2021, BIRN conducted some focused work processes optimisations in an attempt to quantify if and to what extent it was possible to reduce the amount of energy required to produce a metric ton of molten iron. Through these tests, they were able to reduce their energy consumption from 640 kWh to around 570 kWh per metric ton of molten iron produced.
The small tests we conducted reassured us that there is a lot of potential for energy efficiency gains to be leveraged when compared to how we operate today.
Lars Jørgensen.
“Another clear benefit of the increased energy efficiency focus is that as we use less energy per metric ton of molten iron, we emit less CO2e. It is critical to us that we actively contribute to reducing our company’s carbon footprint,” says Lars Jørgensen.
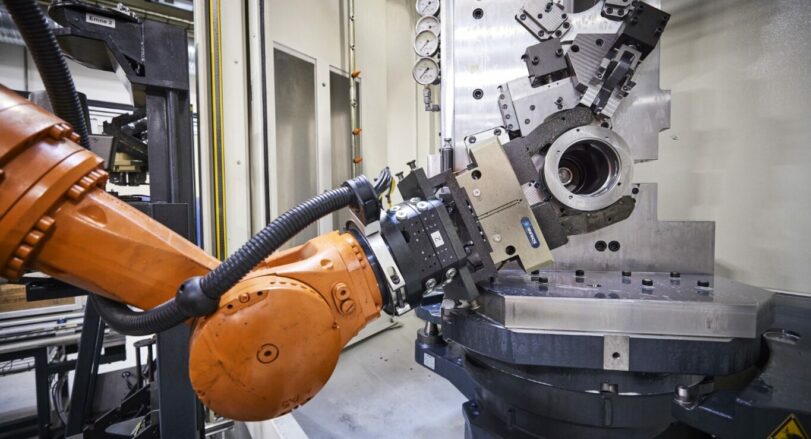
People – and data availability – are key to energy efficiency
BIRN converts scrap metal into molten iron in large induction furnaces. The induction capability of the iron mass is not consistent throughout the melting process. For instance, the induction capabilities significantly decrease in certain temperature ranges, so it’s crucial to closely monitor how the furnaces are operating.
When operators are responsible for multiple furnaces dispersed across a physically large shop floor, it can be difficult to obtain updated insights. “An ideal melting process, where the oven is emptied for the molten iron, is characterised by having a steadily increasing cumulative energy consumption from beginning to end,” Lars Jørgensen adds as he continues. “If the accumulated energy consumption curve has long ‘flat periods’, this indicates that the melting process was not ideal.”
The collaborative innovation project that BIRN completed with Init uncovered, among other things, a wide range in the energy efficiency of each melting process. Moreover, thanks to machine learning, various clusters with various cause-and-effect relationships were revealed.
From production data to actionable information
Based on our findings, it was evident that an operator tool was needed. Throughout the course of a workday, the operators must complete numerous tasks at various furnaces and melting processes. The amount of energy used in a melting process is greatly influenced by the operators.
To meet this challenge, Init developed an operator dashboard which is available on a tablet installed in the operator’s truck and serves as an anchor point for their work. The dashboard contains a few, but extremely important pieces of information. Thanks to the real-time insights the dashboard enables operators to respond quickly when a melting process needs their attention.
Additionally, and in close collaboration with BIRN managers, Init has developed several different reports to give BIRNs management team a better understanding and overview of energy efficiency in the production. One of the most important reports provides an overview of energy consumption in kWh per metric ton of molten iron, as well as an overview of how long the energy consumption flat periods have been. The reports can be aggregated, drilled into, and then sliced and diced so that management can get a broad picture and detailed insights from a single report.
Adjusting work procedures for higher energy efficiency
Even with a trained eye, it can be challenging to find patterns in massive amounts of data with numerous different parameters. For the purpose of finding patterns in data, Init employs machine learning tools. This knowledge is used to direct operators and management in their pursuit of energy efficiency in day-to-day operations.
The insights provided by data-driven services allow BIRN to validate and improve their standard operating procedures (SOPs) for the purpose of energy efficiency.
Depending on whether there are fewer people on a shift than usual or if there is one less furnace to operate than usual, there may be some variation in how the work should be carried out. Lars Jørgensen says, “Based on our learnings from historical experiences and with the real-time insights the operators have with the new tools, it is much easier for us to execute our work with energy efficiency in mind at any time, regardless of the working conditions.” He adds, “If some of the normal working conditions change, it is much easier for us to guide operators as to how they should execute their work.”
Paving the way for continuous improvement
With the implemented solutions, BIRN has achieved not only lower energy use and a smaller environmental impact but also higher employee engagement. But for BIRN, energy efficiency is a continuous process, and new possibilities arise constantly. The data-driven insights provide a common foundation for the entire BIRN organisation to optimise work procedures.
“We see a lot of exciting opportunities ahead. Some initiatives concern energy efficiency, while others are complementary. For example, going forward, we will be able to incorporate energy prices and anticipated energy needs into the production planning processes thanks to our increased data focus and improved data quality”.
Even though our change initiatives are based on us running a foundry, I am convinced that there are similar opportunities for other companies in other industries with data-driven insights and services.
Lars Jørgensen.
Reach out
for more information
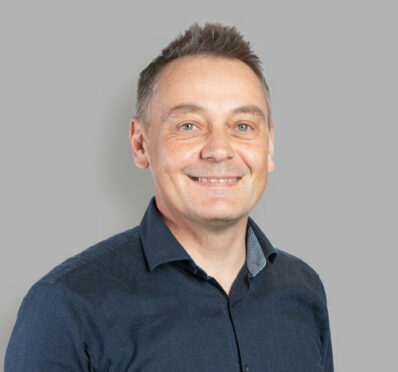